Building:
Construction site (facing south)
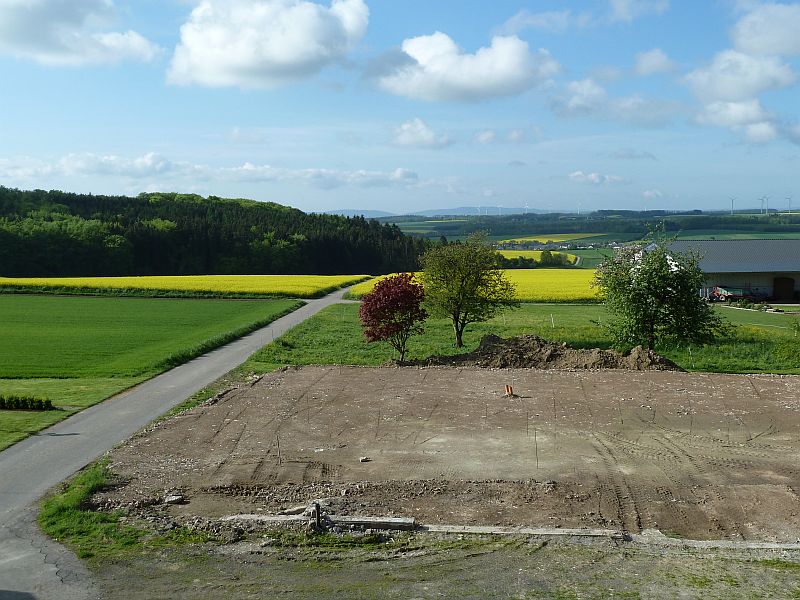
The building ground was professionally filled, compressed and levelled by Otmar Hennchen.
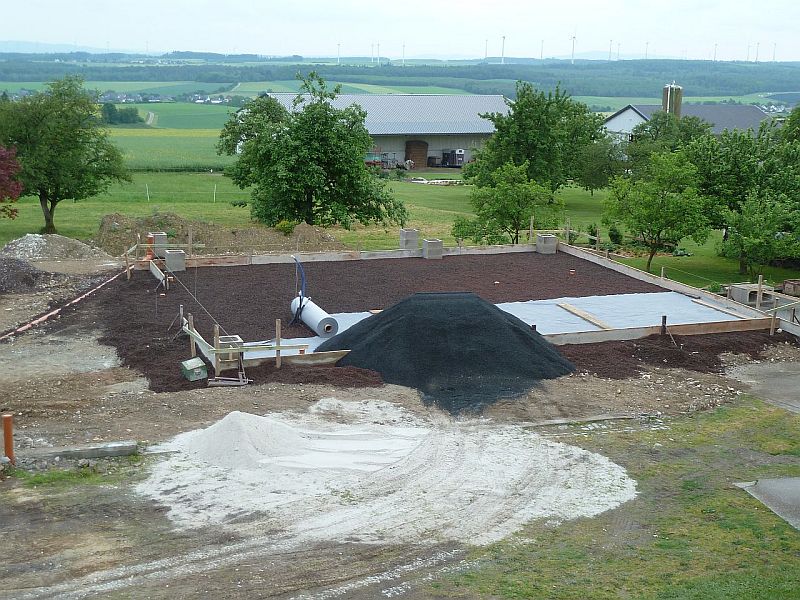
Water, sewer, cable… connections placed, 20 cm Lava as anti-capillary layer, then fleece and 5 cm loose gravel on top.
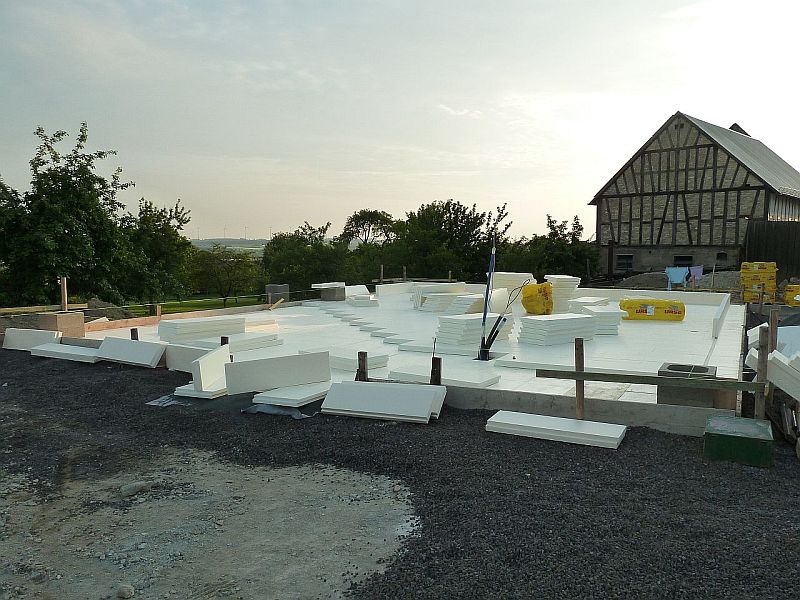
The stay-in-place formwork (insulation) of the base plate is made of 24 cm XPS (hard Styrofoam).
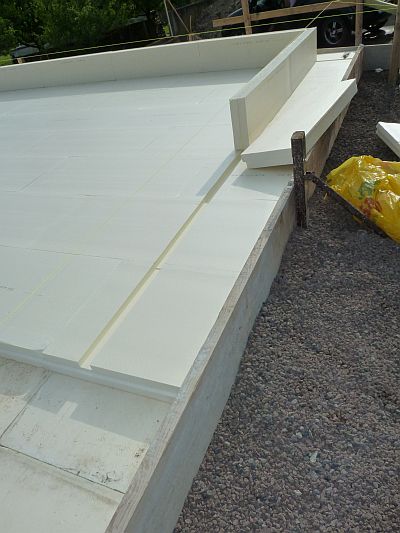 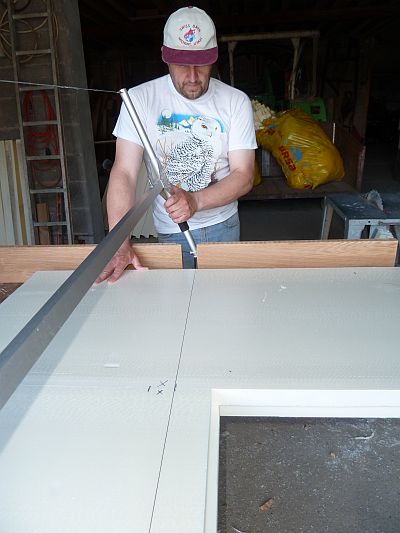
We “hotwired“ the grooves for the perimeter-insulation and left a horizontal frost-protection.
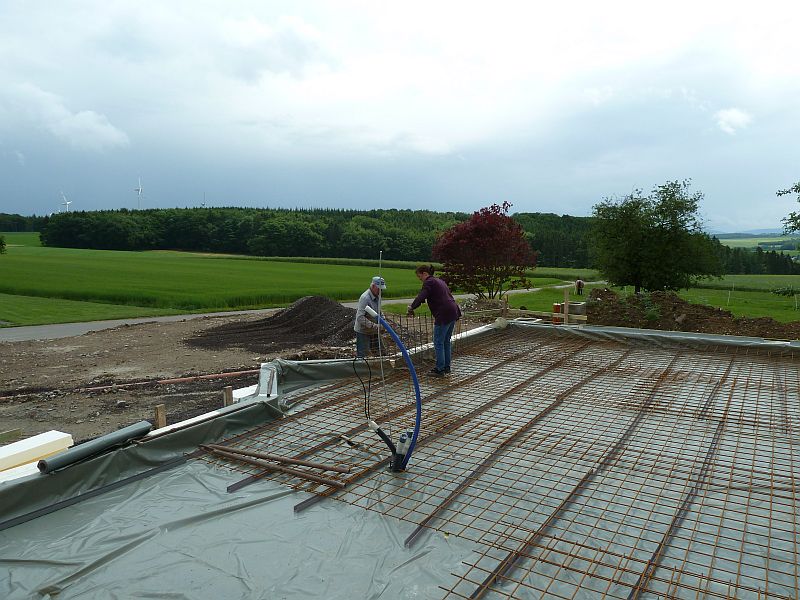
The steel mats (Q 434 A) look lighter than they are...
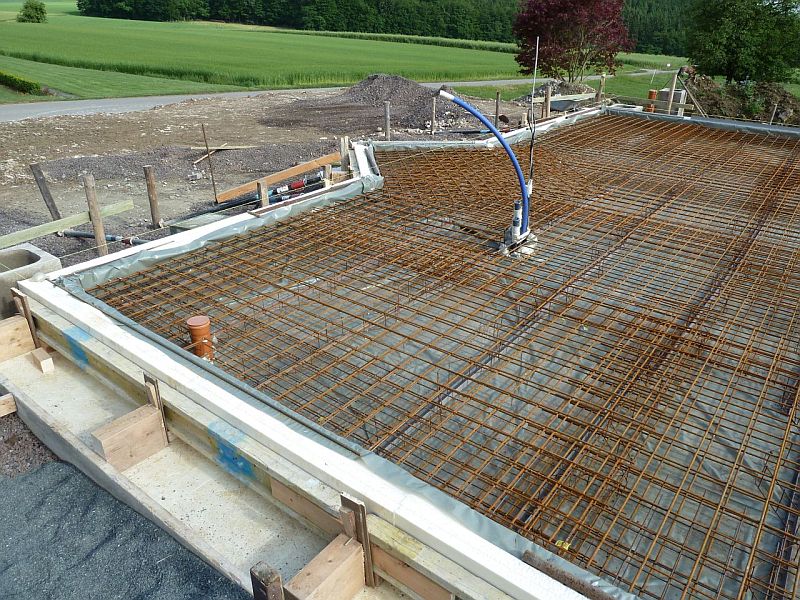
Finished XPS-formwork (240 mm) and steel-reinforcement for the 25 cm concrete base plate…
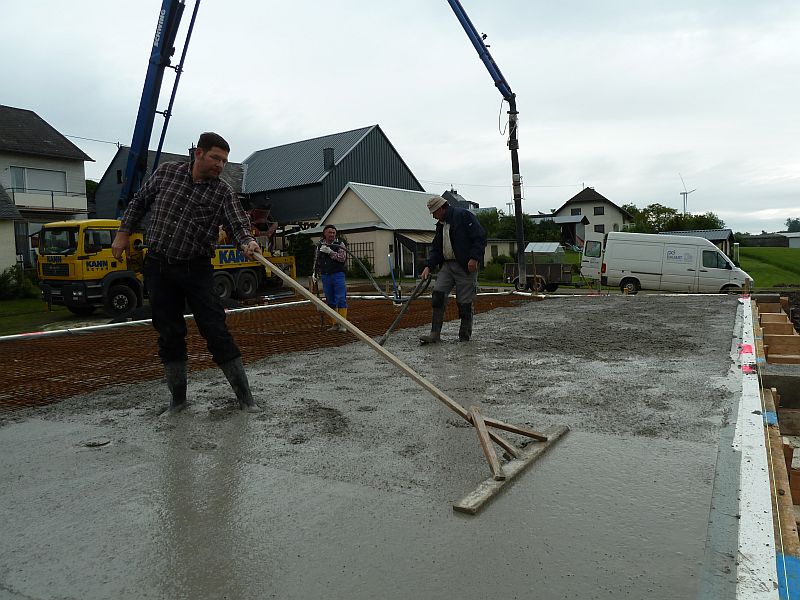
A job for specialists… – support in concrete building from Peter Gräf, Bauart Gräf.
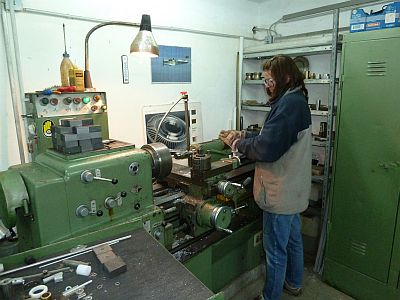 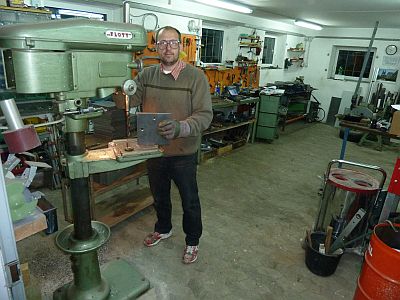
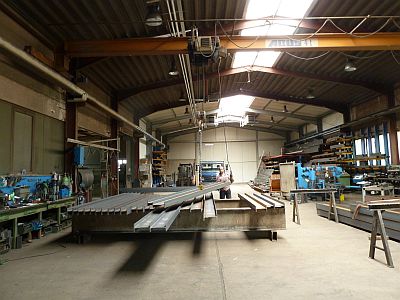 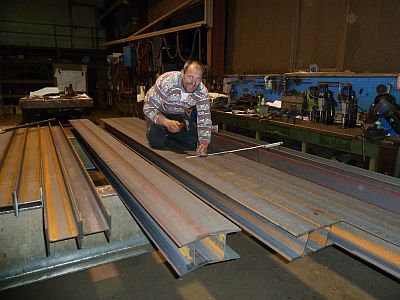
While the concrete sets, we are drilling appr. 1 ton of flanges and pieces for the steel construction in our garage at home (upper pictures). Then we are sorting, marking and drilling 9 tons of steel beams at the production site of Thomas Laube (lower pictures) before the parts are welded. This works paperless out of the notebook (since the builder made the drawings…).
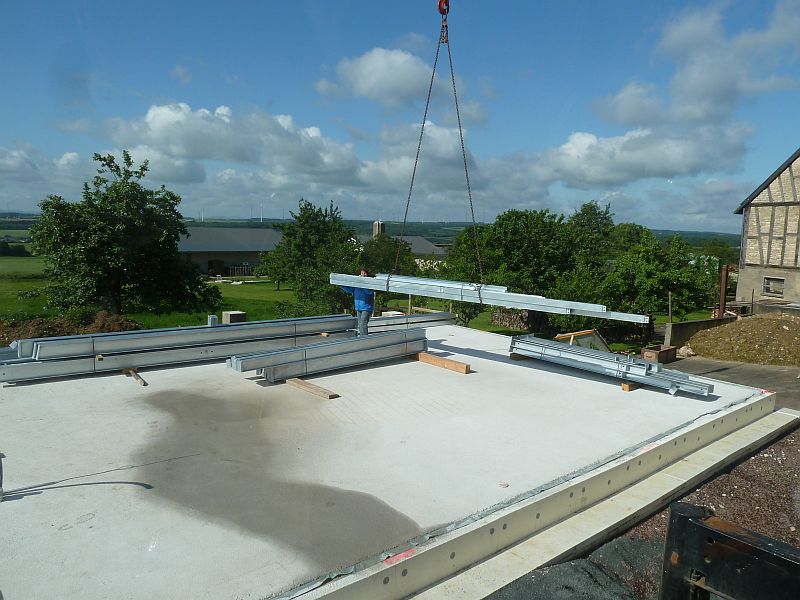
Allways a good team! My wife aligning and me lifting the load (operating the crane).
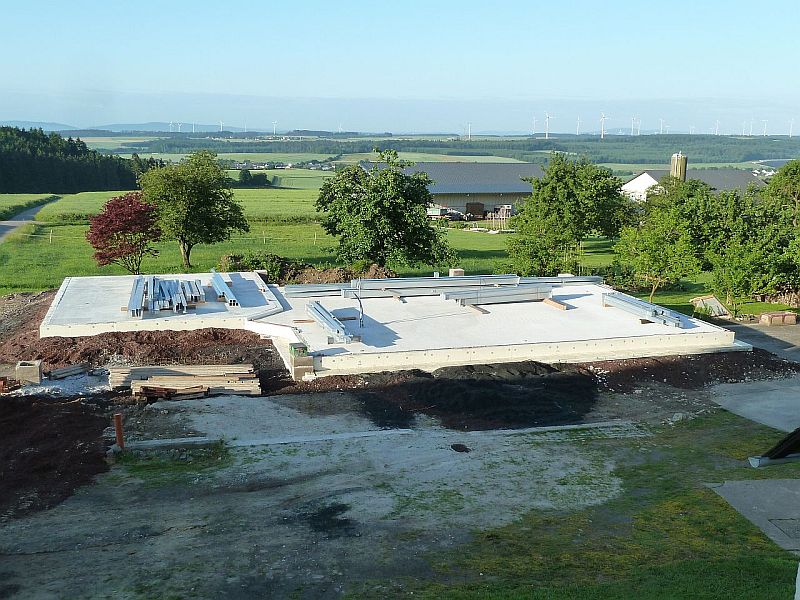
The base plates of the house and the garage are thermally separated. All zinc-plated steel parts (appr. 10 tons).
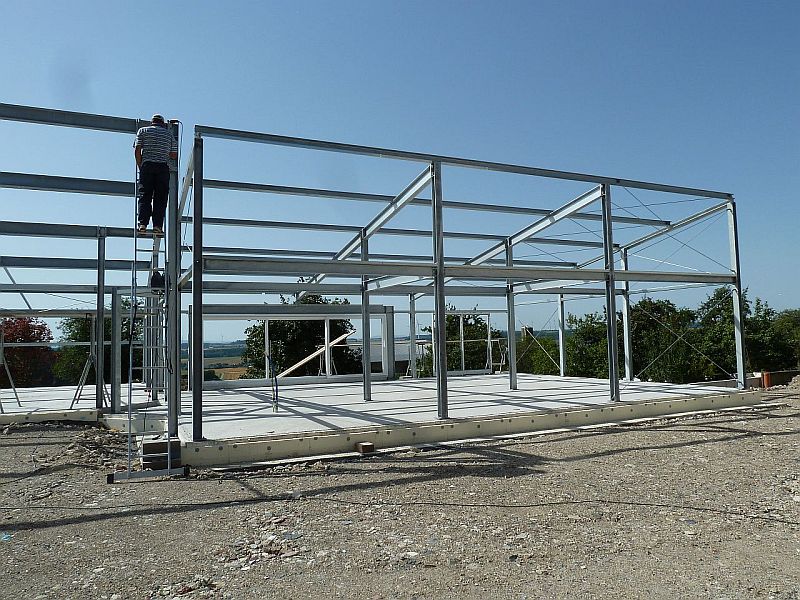
The steel-construction was raised in 1 day. House and garage are separated (no thermal bridge).
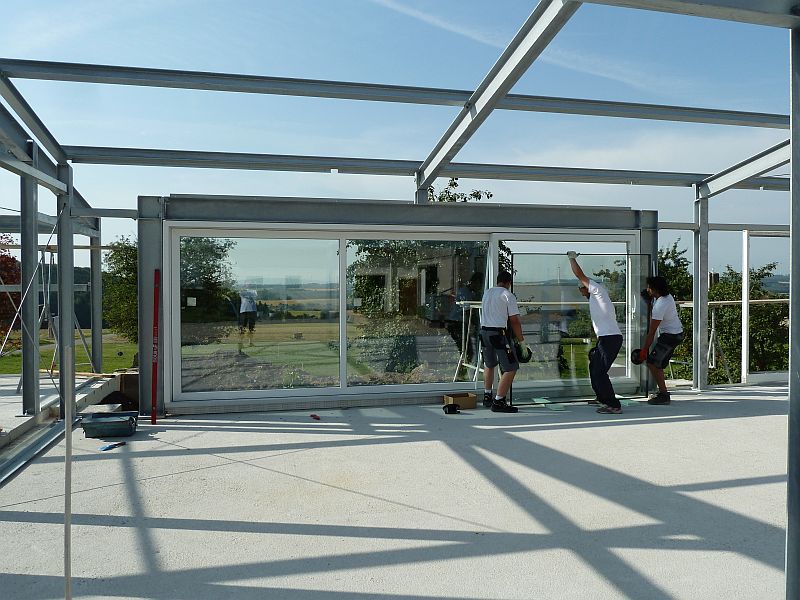
Installing the 147 kg 3-layer thermal glass into the windows supported by our window contractor Günther. Unconventional, like other details on this project, window-installation prior to roof and walls…
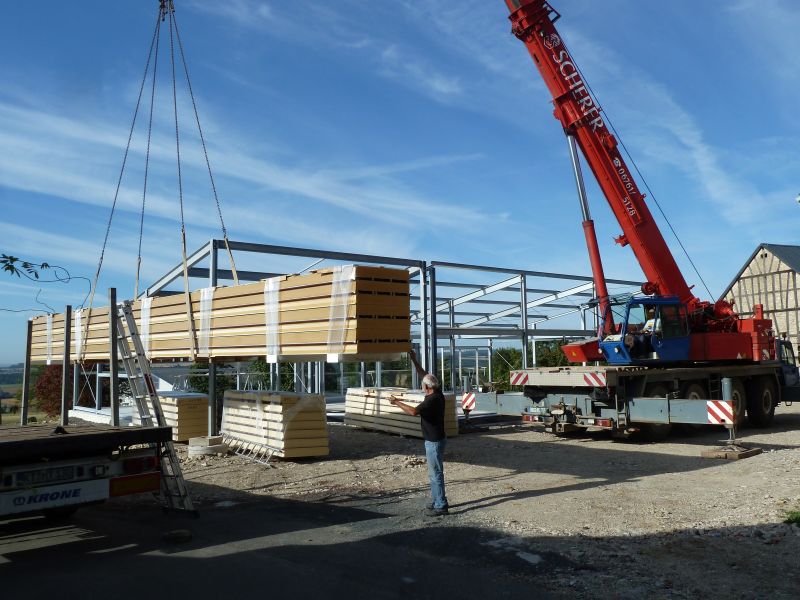
Delivery of the sandwich-elements. The crane I am operating is provided by Erwin Scherer. Do it yourself definitely pays off.
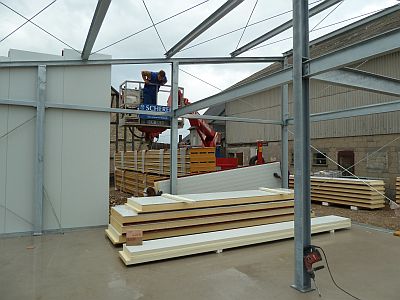 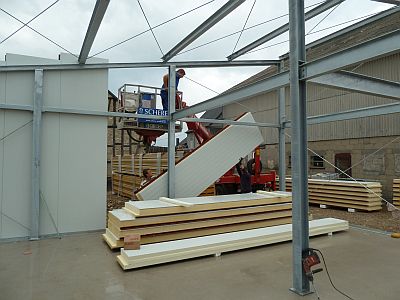
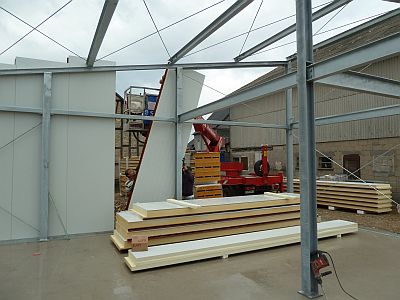 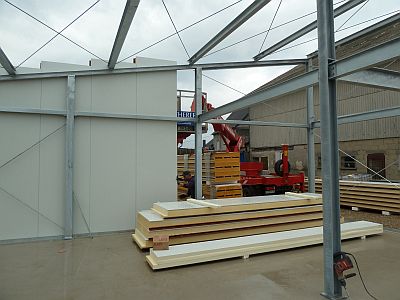
We were able to raise all of the wall-elements with 2-3 workers and a man-lift from Scherer.
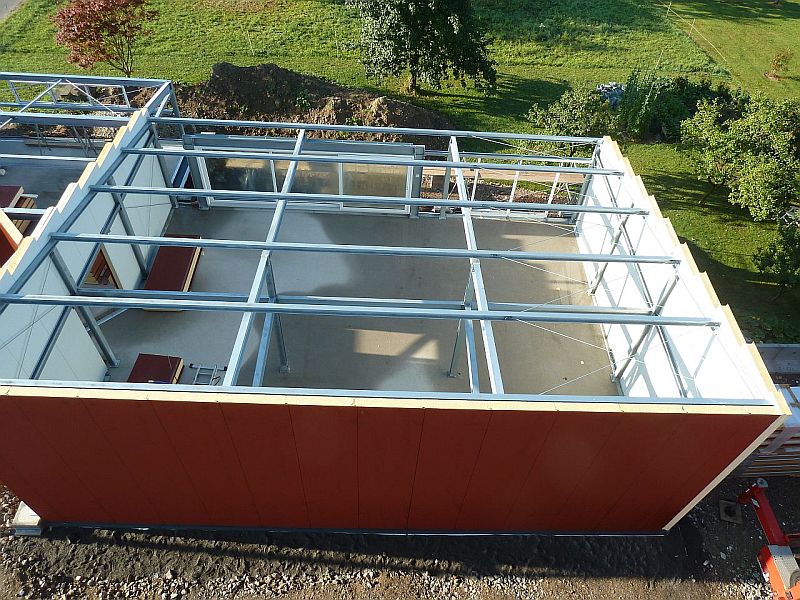
Fastening (covered – bolts not visible) the sandwich-panels (Romakowski - wall M170 - U-value by EN 14509 = 0,147), outside insulation, finish and painting of the home are done in 1 step. At 17 cm wall-thickness the U-value meets passive-home-standard already!!!
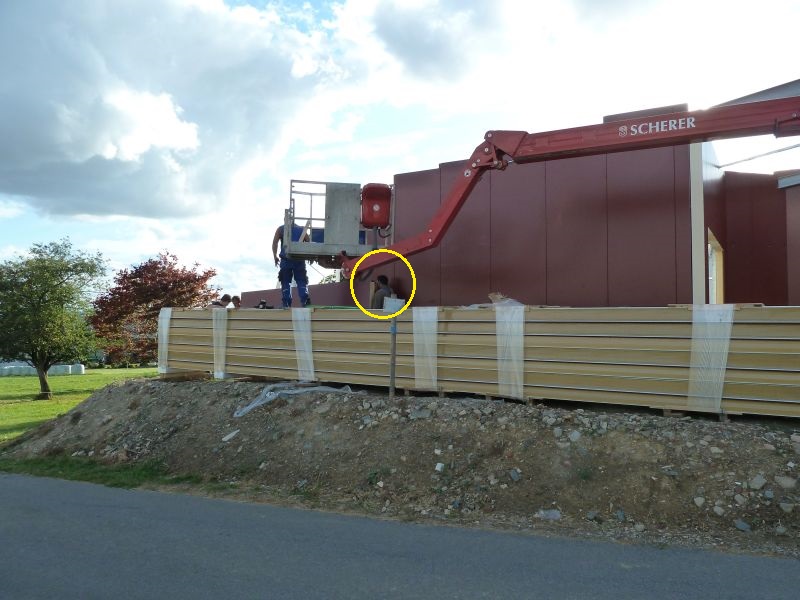
Even the boss gives a hand at Laube steel construction!
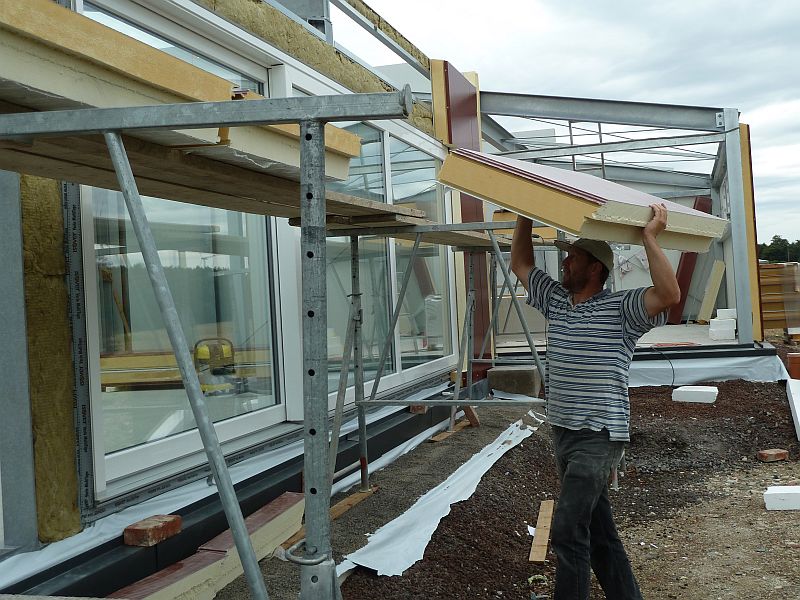
Cutting and mounting the smaller panels (17,1 kg/m²) works out alone.
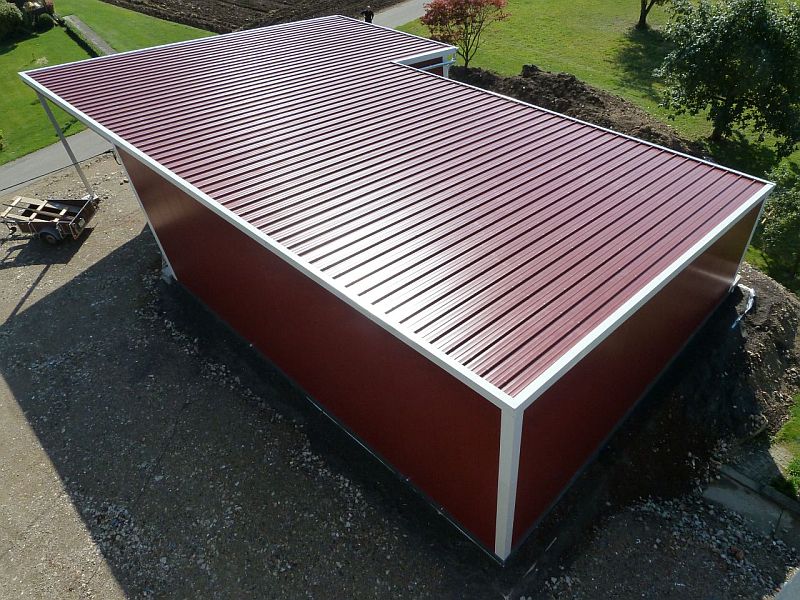
The roof-panels (Romakowski - roof D 182 U-value by EN 14509 = 0,169). Additional windows and the main entrance will be cut out and mounted later...
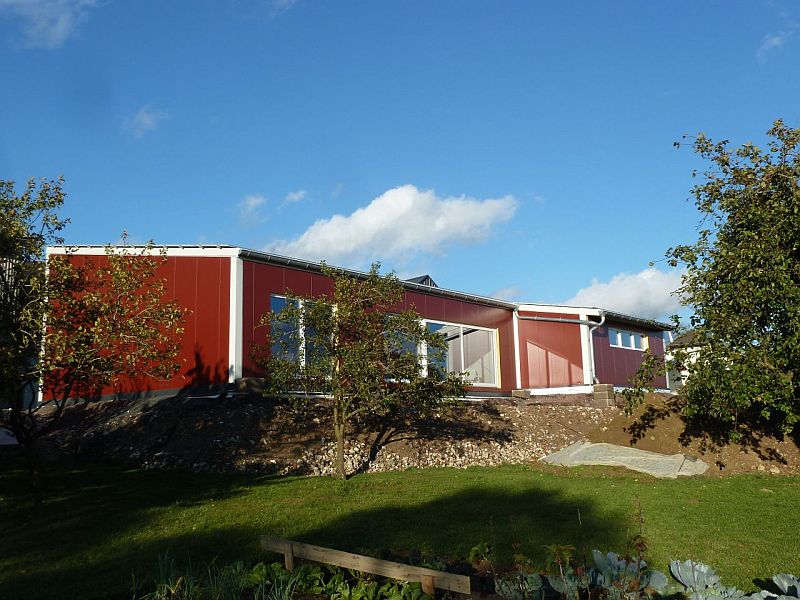
Only the sun trough the south facing windows is heating the construction site for now.
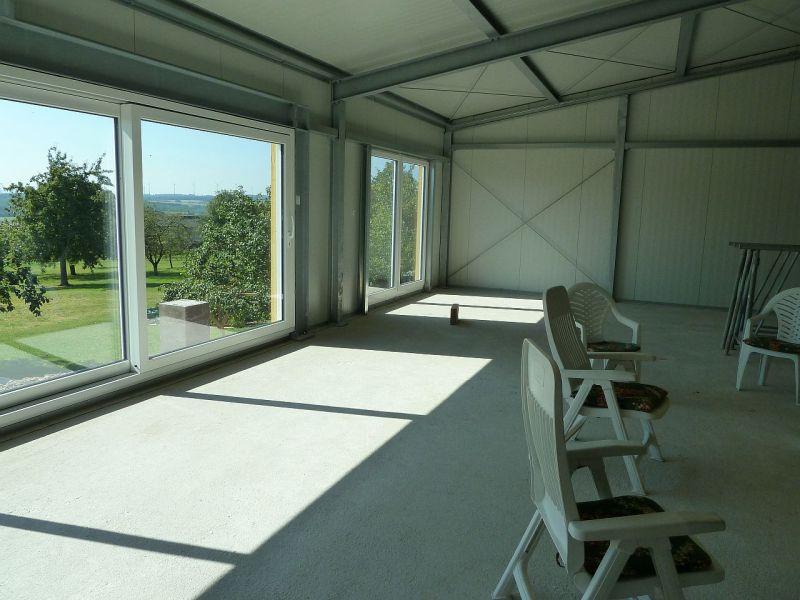
The steel construction is completely inside the sandwich-shell and serves as additional insulation and installation space (power, water…).

Quiet place heading south…
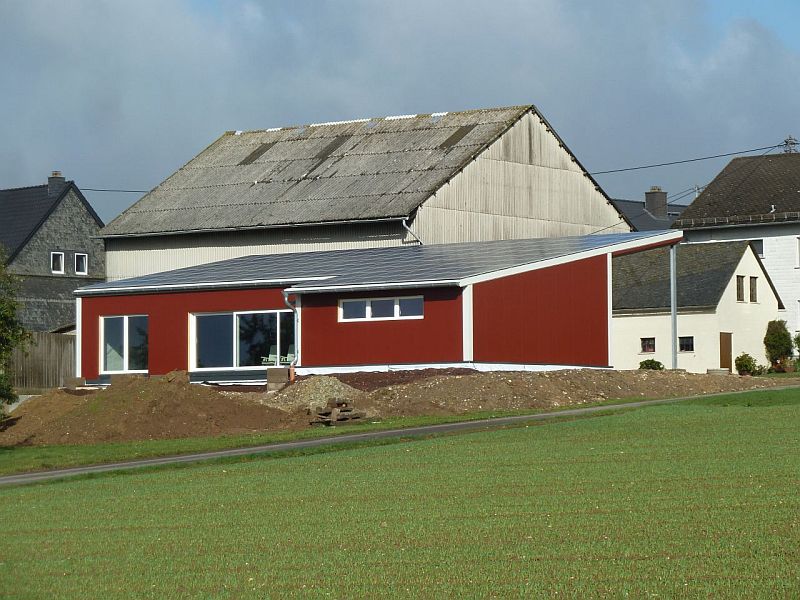
Lean-to roofs are becoming popular for homes in Germany and the advantage for solar use is evident. A positive energy footprint is guaranteed having 35 KW (peak) solar-power installed.
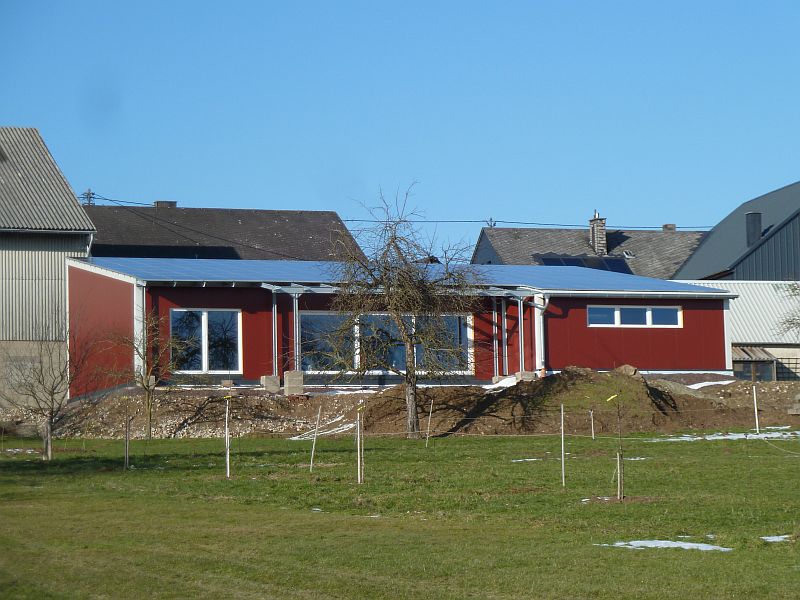
Above the terrace, the solar panels are overhanging by 1.5 m to allow the low sun to heat through the windows during the winter and spend shade for the windows in summer.
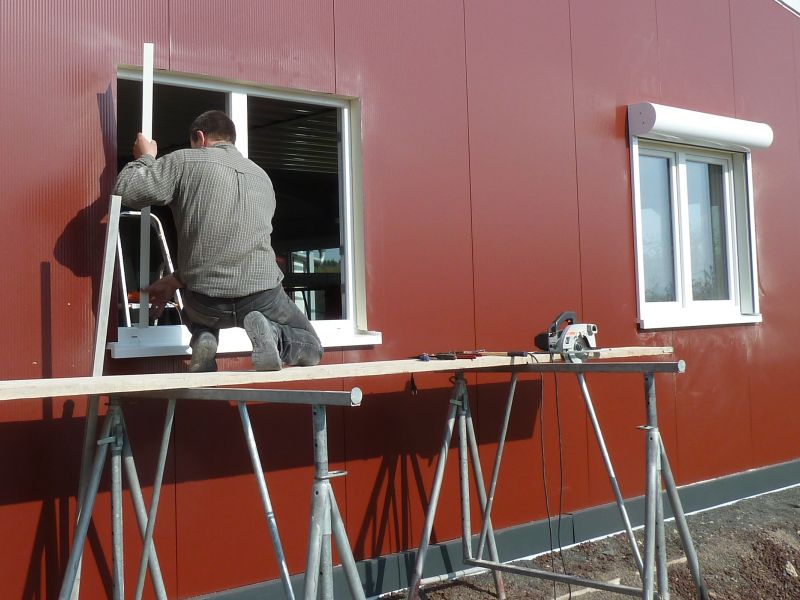
Installation of the remaining windows (these are facing west)...
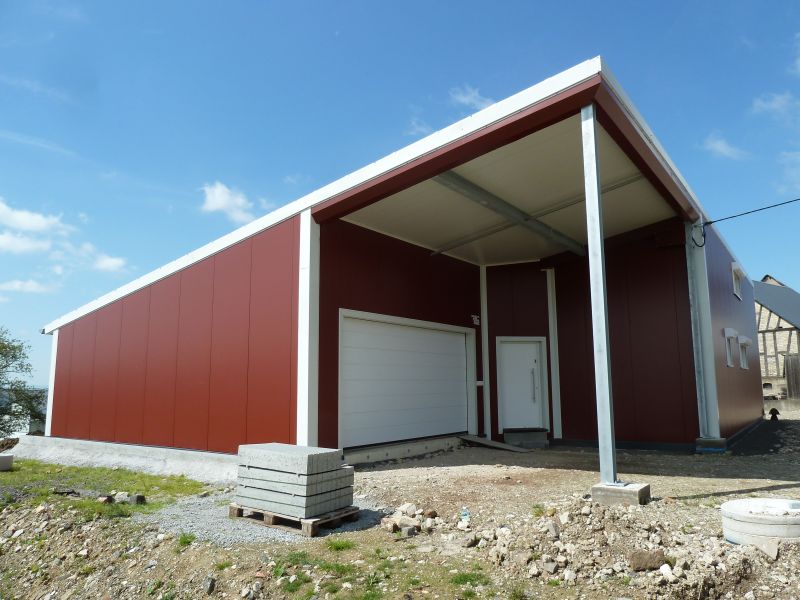
...main entrance (facing north-east).
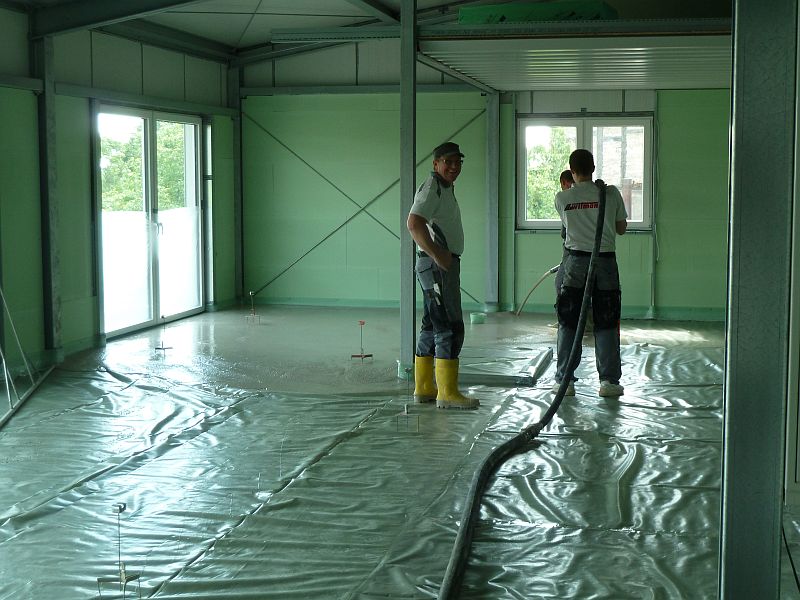
Alexander Witmann is applying the floating screed.
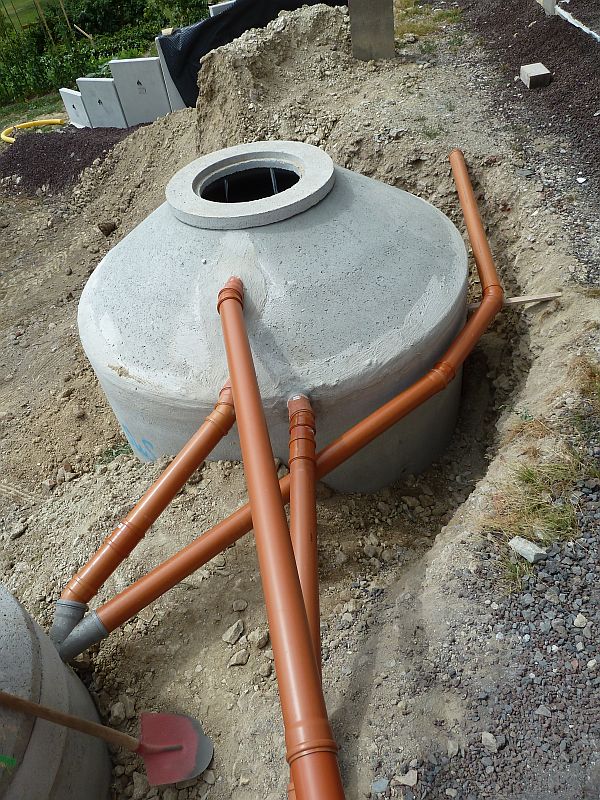
The cistern from Aquaroc is connected...
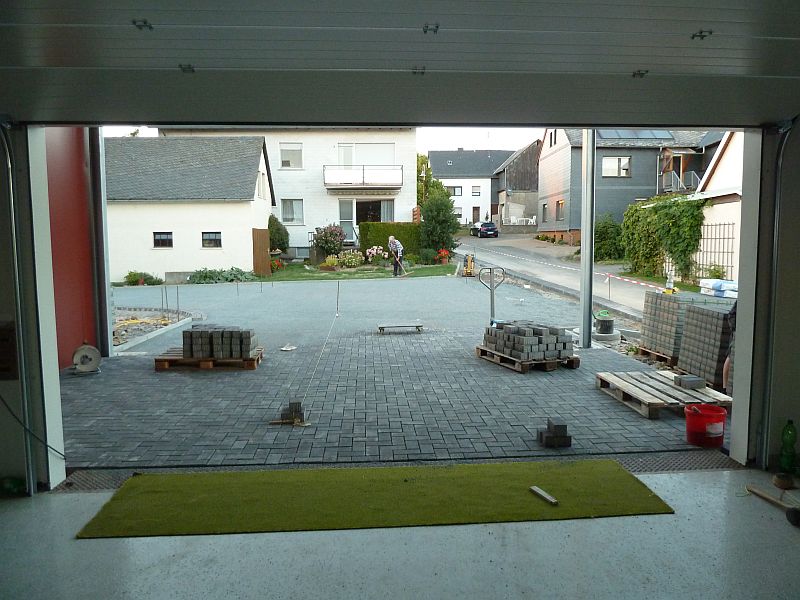
Following the preparation and support of Thomas Eppert, we laid about 270 m² block pavement.
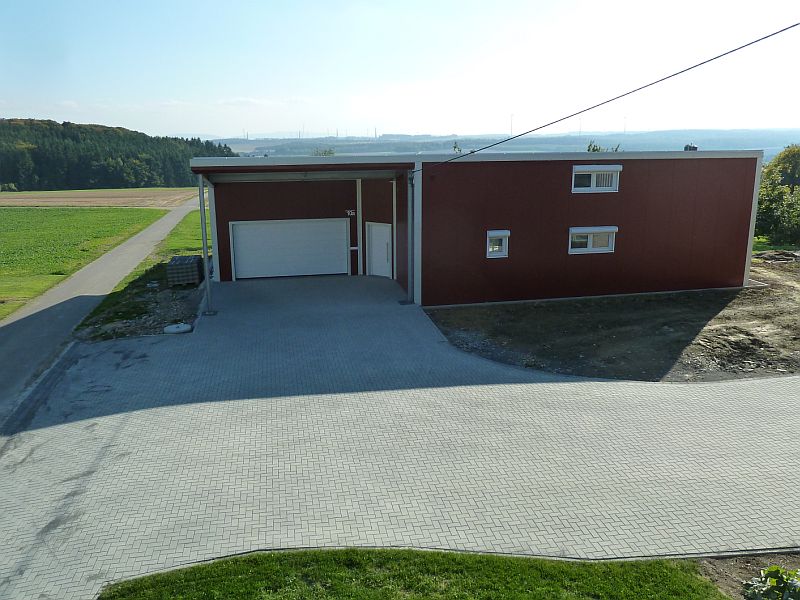
The driveway got finished just prior to the winter. We will work inside now...
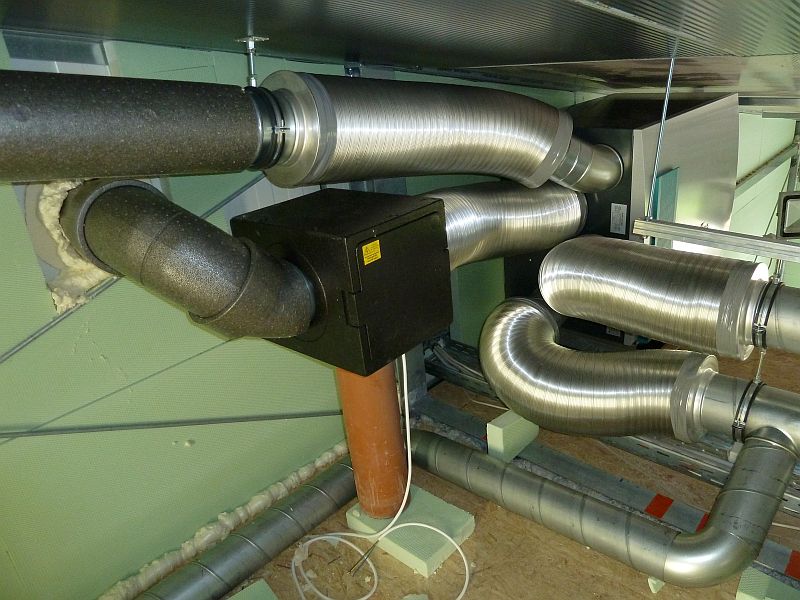
We installed the ventilation system with heat recovery.
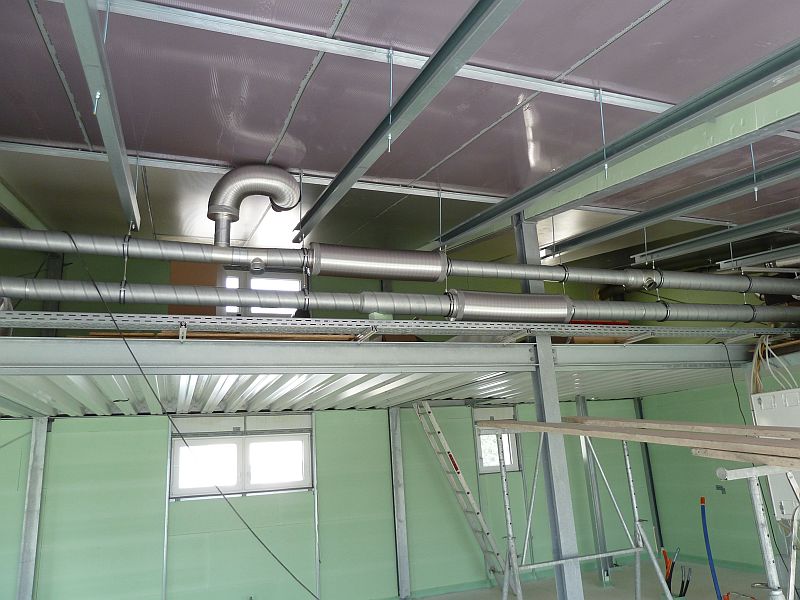
Still visible, the auxiliary space for power, network and ventilation system will be accessible from the upper storage room.
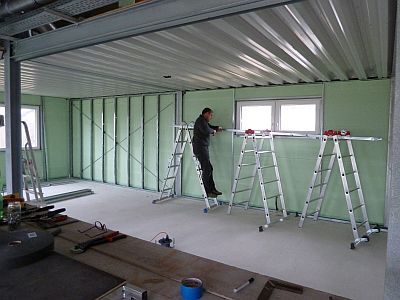 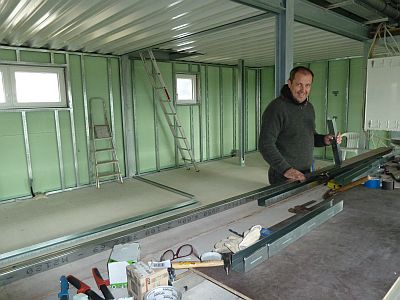
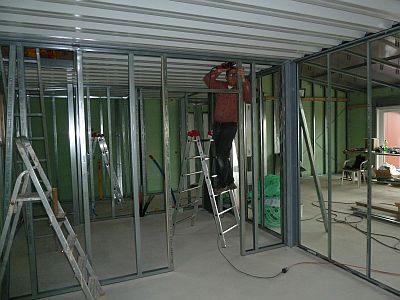 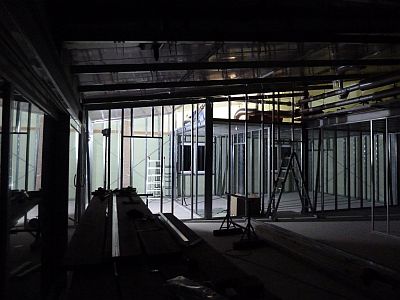
Drywall installation – mounting the first UW and CW – channels. Then continue until you miss the forest for the trees.
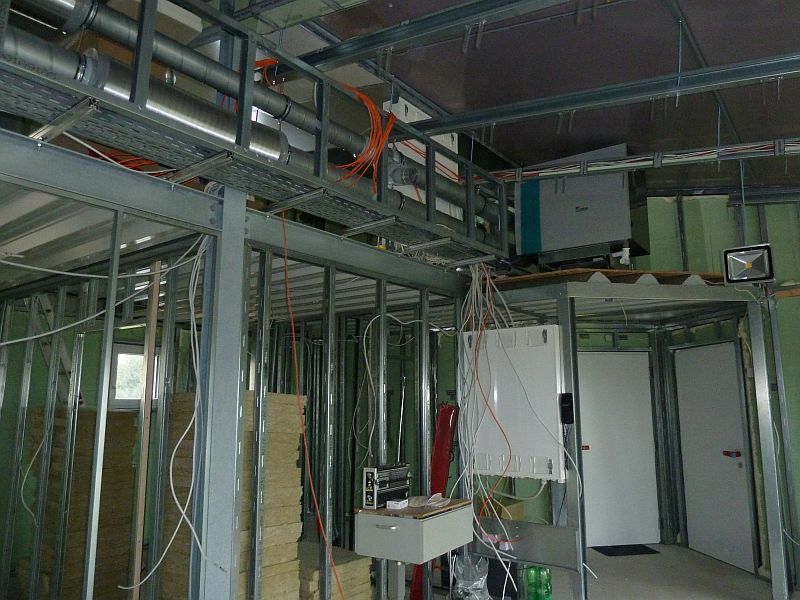
Here we are, installing the wiring & network before the sound absorption material (rock wool) can be installed.
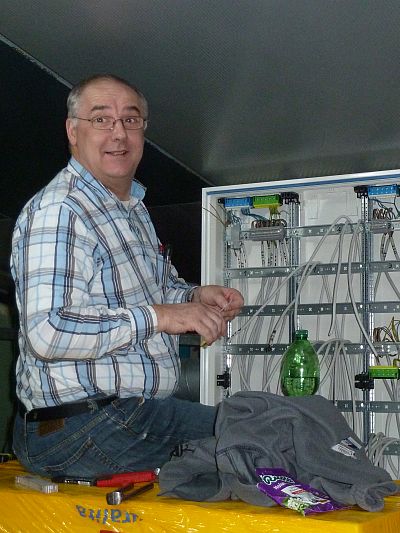 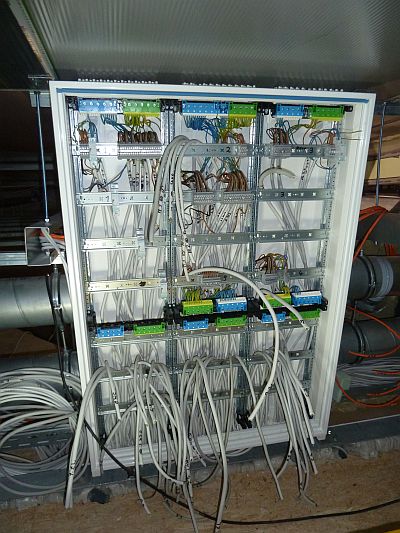
Our friend Thomas Pohl is helping with the electricity. This is how it looks like if you would like to connect every switch and each socked in every room independently and not all of the 2000 m cable arrived her yet.
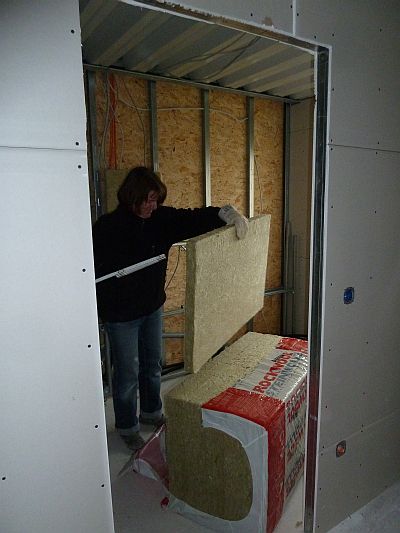 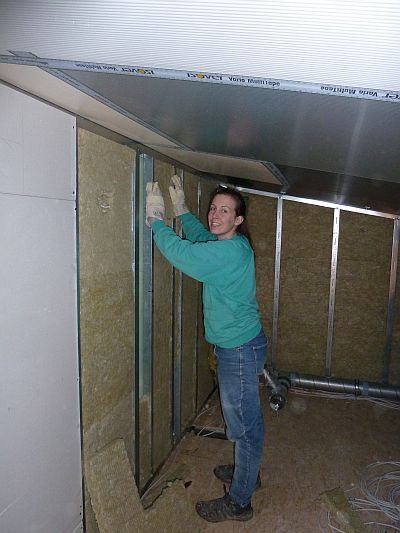
Teamwork applying the rock-wool to all outer and inner walls (sound absorption).
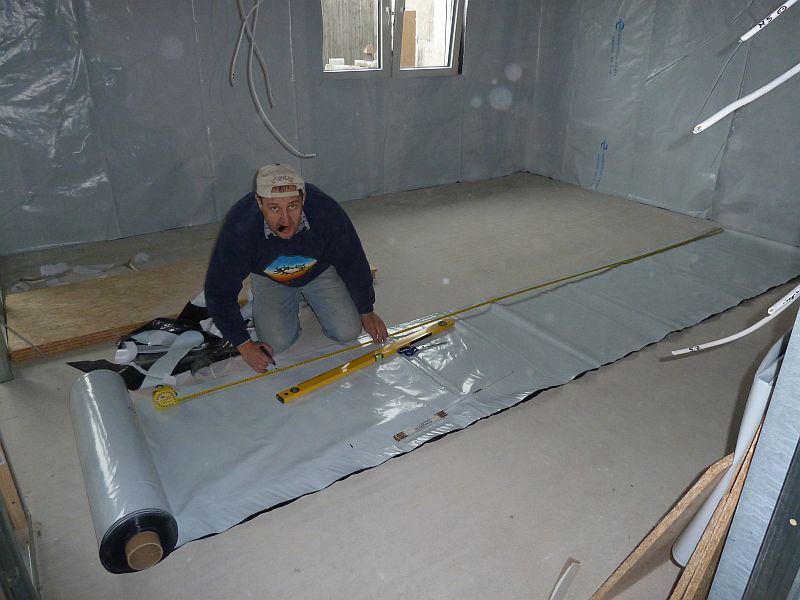
We are applying a foil (inner vapor barrier) between the two layers of sheetrock.
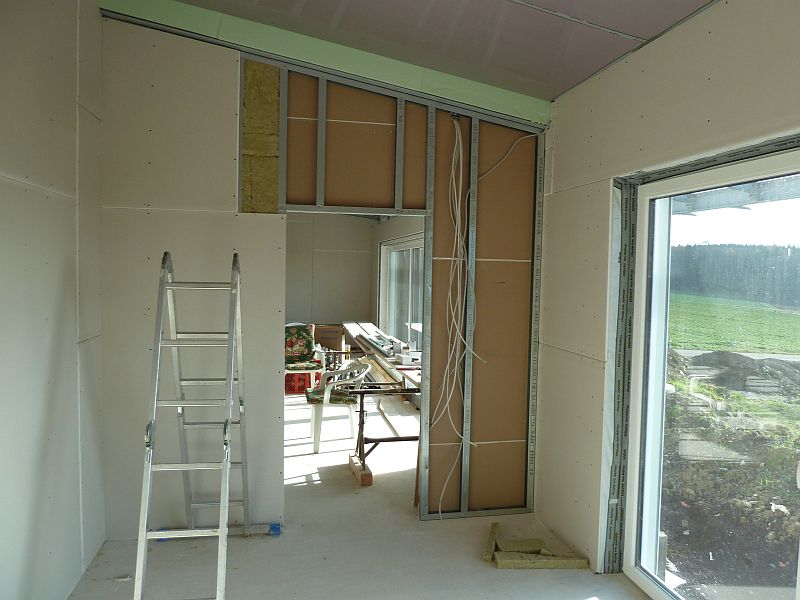
Following the second layer of sheetrock on the outer walls we are completing the inner walls.
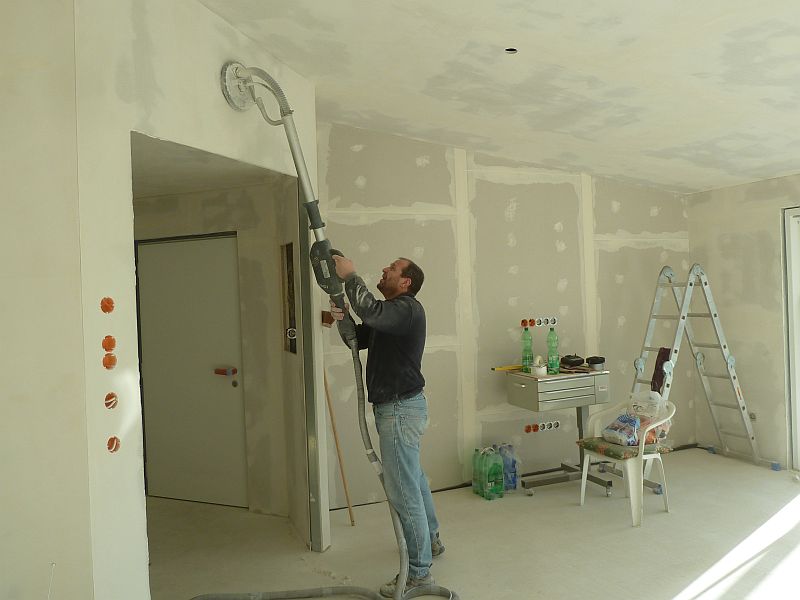
Despite the vacuum cleaner being connected to the machine, this is a very dusty job.
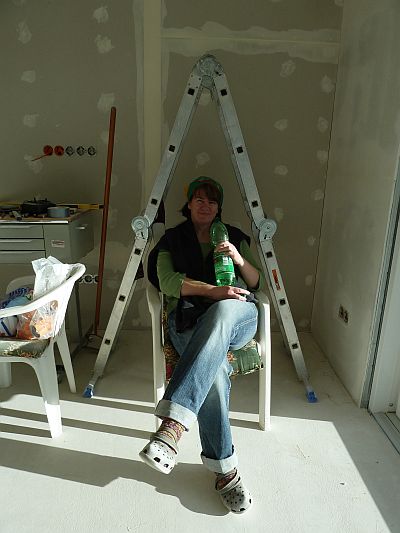 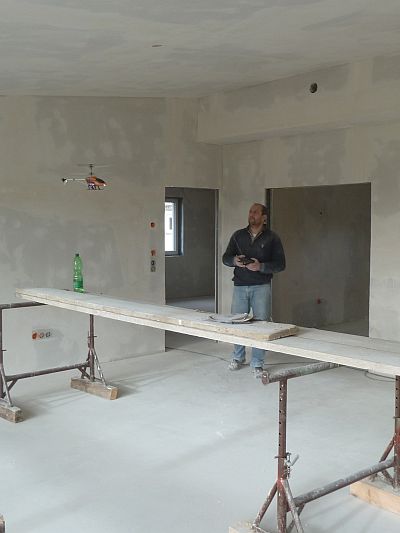
Performing exhausting jobs we need a brake – everyone in her/his way...
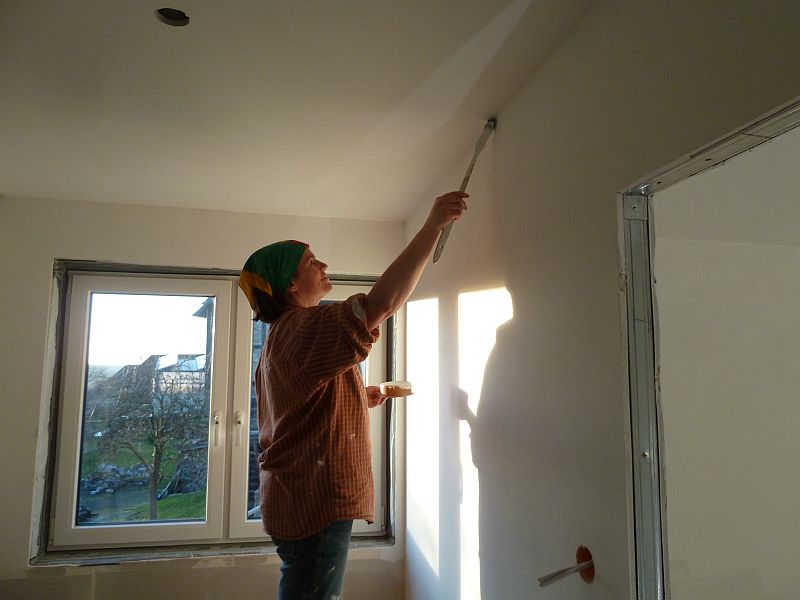
Painting is almost a clean job (following the dust of grinding). Klaudia is preparing the edges…
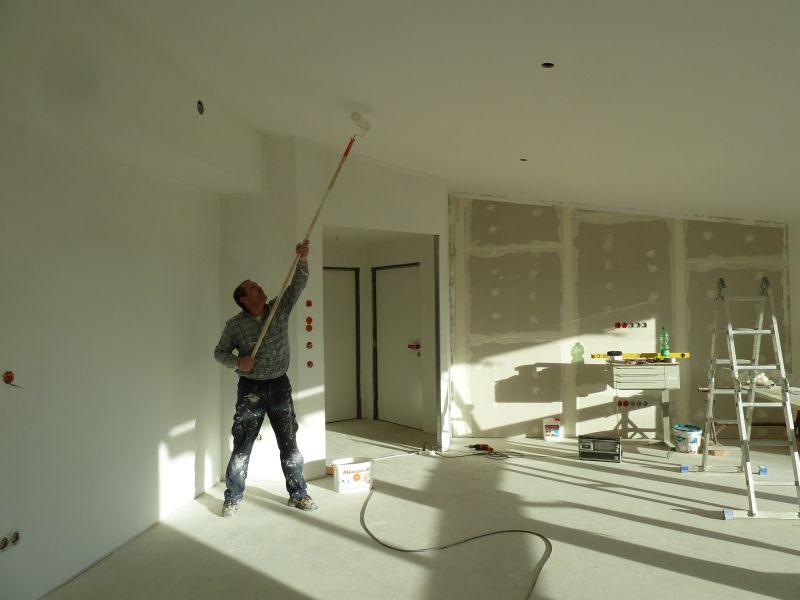
... and Wolfgang paints the areas.
This is how our “energy-plus home made of steel” looks like:
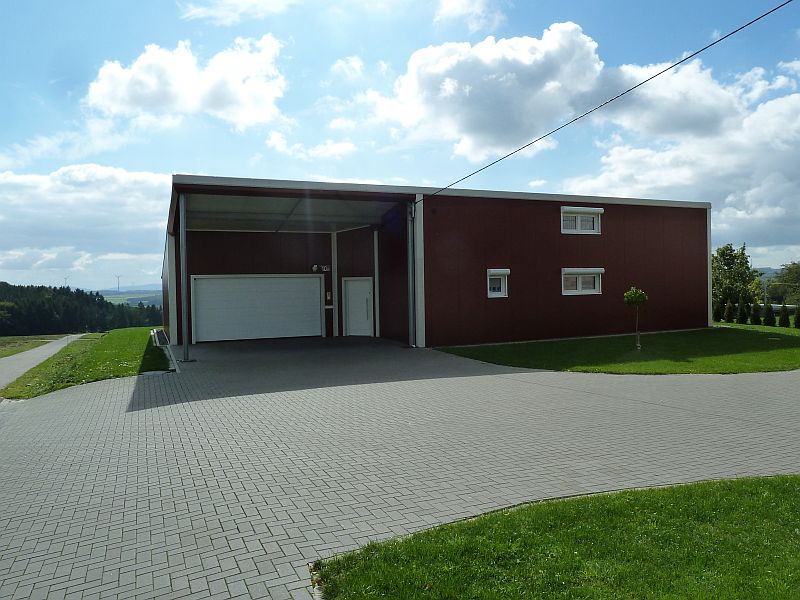
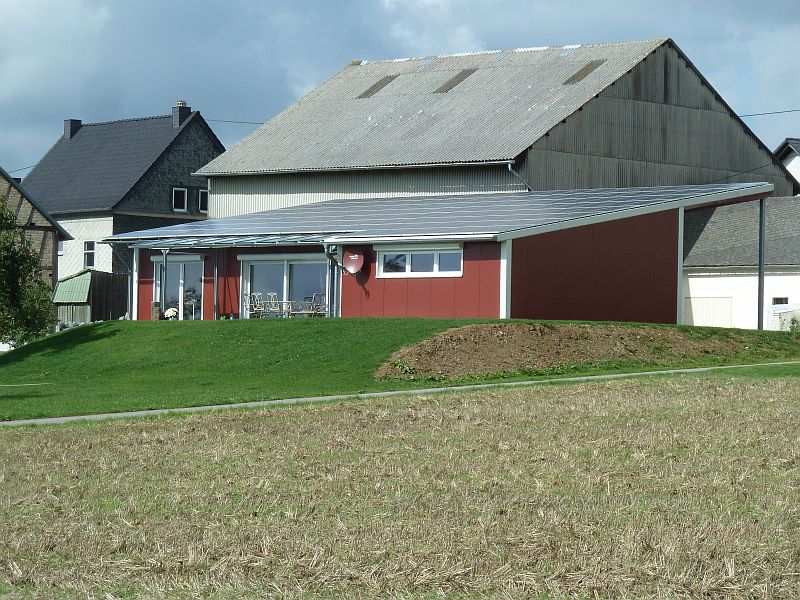
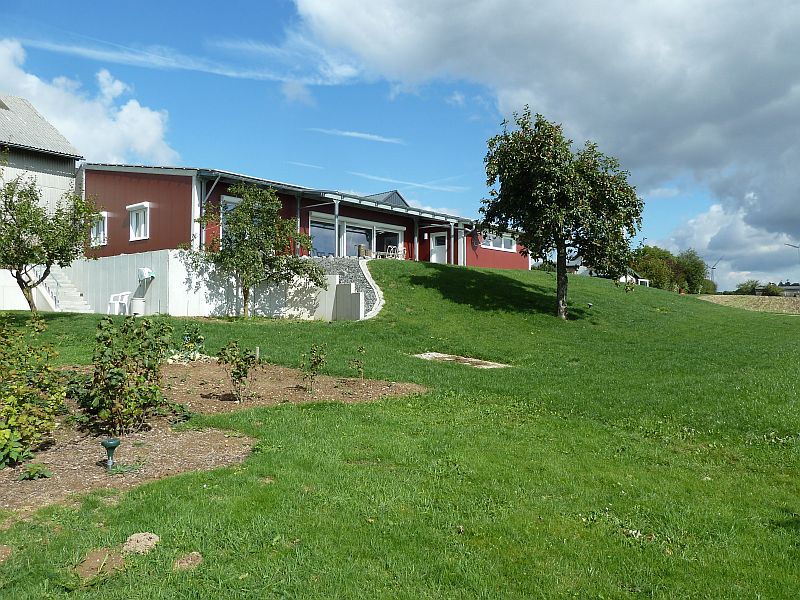
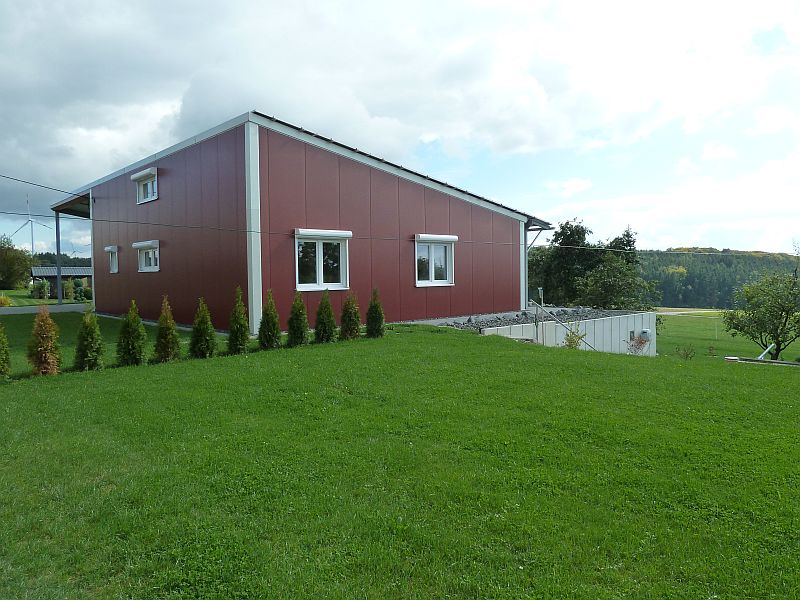
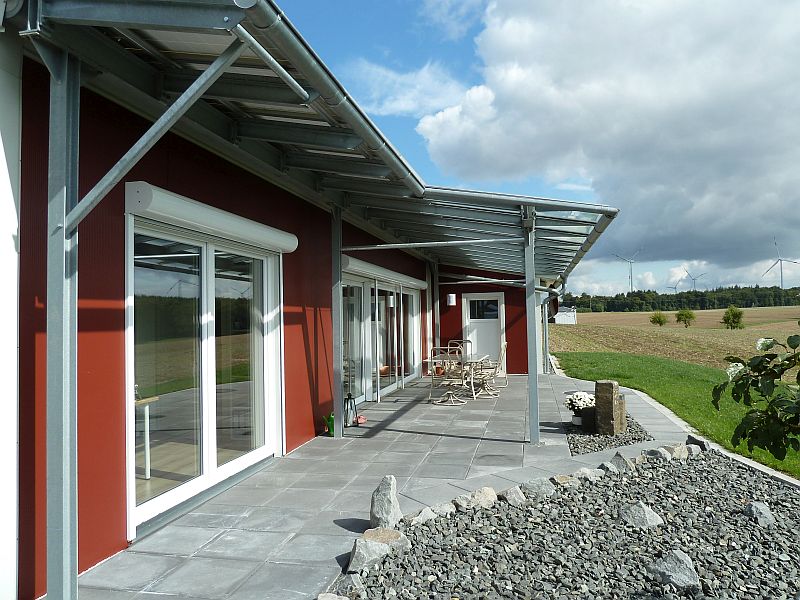
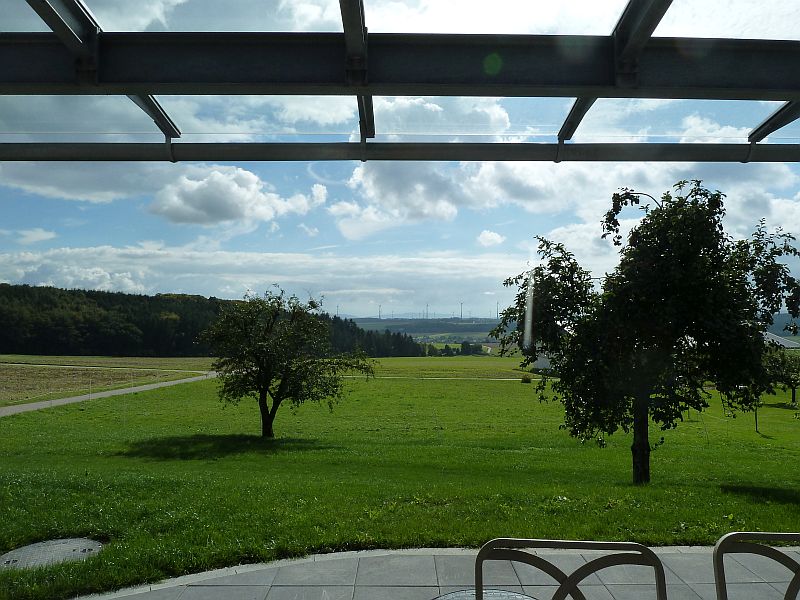
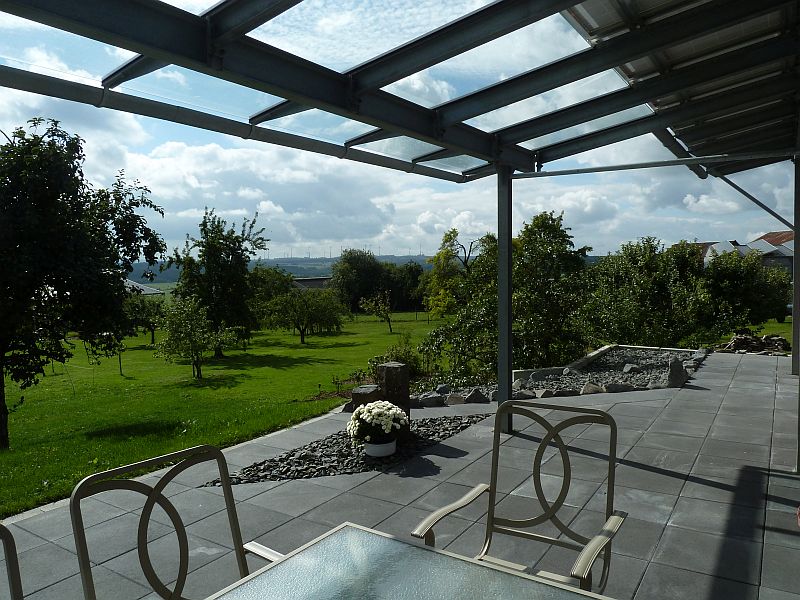
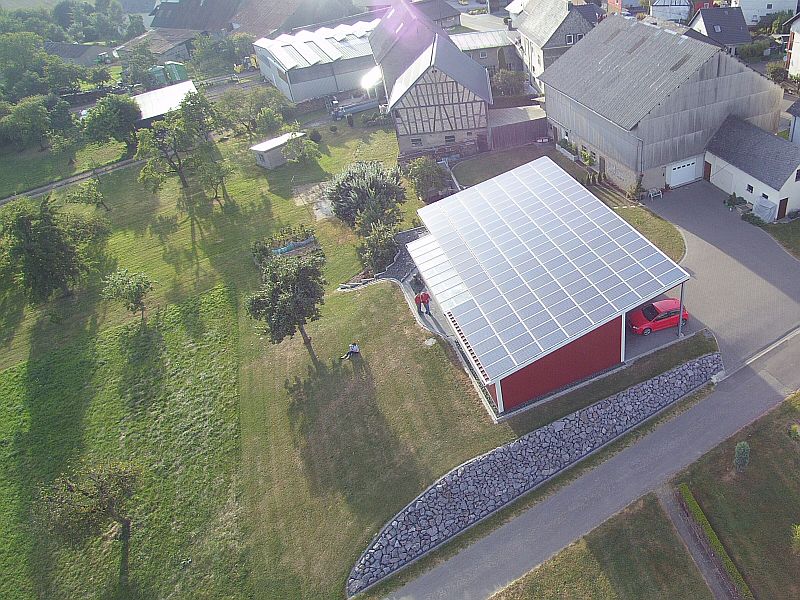
|